Welcome to week three of Gazelles Off-Road “Project Purdey”, where the workshop buzzes with progress, problem-solving, and the satisfying hum of technical tinkering. The past week brought challenges along with some exciting technical advancements as we push closer to our goal the workshop buzzes with progress, problem-solving, and technical solutions.
Front Differential Rebuild: Precision and Sealing
At first the Gazelles Team focused on the front differential, carrying over lessons learned from last week’s work on the rear diff. The process started with a thorough clean-up to ensure no contaminants interfered with the installation.
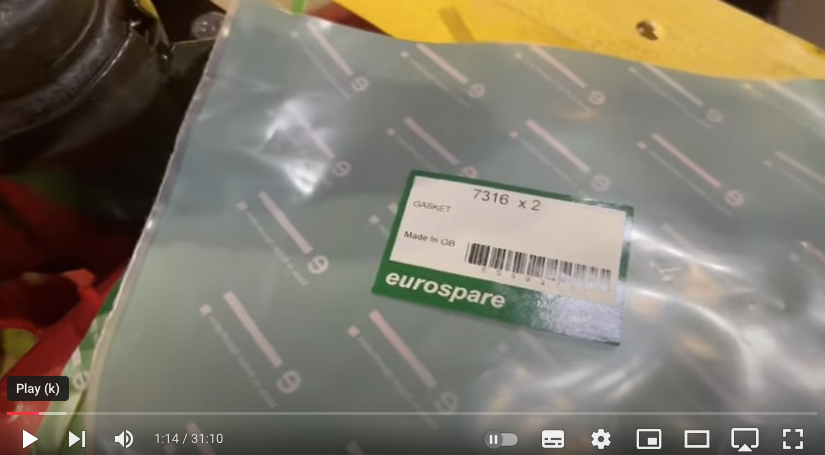
The team used a eurospare gasket, which provided a precise fit. To bolster reliability, a layer of silicone was applied, particularly around the lower edges where oil leaks are most common. It’s a small but crucial detail to mitigate one of Land Rover’s well-known quirks.
Key technical note: The fasteners for the front differential are UNF-threaded, a detail worth remembering for future repairs or replacements as this differs from modern metric standards.
The most intricate part of the week was the attempt to position the engine into the chassis. With the gearbox still attached to the engine, balancing it on the crane proved challenging due to weight distribution. To address this, the team temporarily lowered the chassis by removing the springs, which will allow for easier alignment.
Technical Challenge: The chassis bolt holes for the engine mounts appeared obstructed by residual galvanization and powder coating. To resolve this, the technician used a thread tap to clear out the threads and ensure proper bolt alignment. A critical step, as forcing the bolts could damage the threads.
The braking system saw significant upgrades this week, starting with the removal of old hubs and bearings from the front axle.
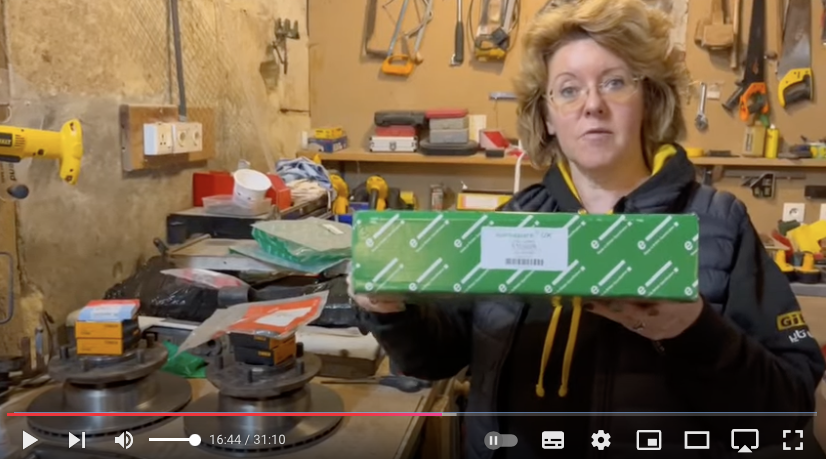
New eurospare vented discs were installed, providing improved heat dissipation and braking efficiency under load. These are a step up from the original solid discs, specifically chosen to handle the increased demands of off-road terrain and rally conditions.
Why vented discs?
During hard braking, especially with added vehicle weight and momentum transfer to the front axle, heat builds up quickly. Vented discs allow for quicker cooling, reducing the risk of brake fade and ensuring consistent performance.
This week also involved addressing the seat box, salvaged from a V8 model. While structurally sound, its tunnel shape didn’t align perfectly with the bulkhead. The issue required reshaping the panel for compatibility.
Additionally, the original battery box, no longer suitable due to the addition of FIA-approved bucket seats, was cleaned and repurposed. The technical challenge now lies in determining whether an access hatch on the side is feasible, which depends on the placement of the future roll cage.
The new backplates for the front brakes were another highlight. Precision-engineered by eurospare, these backplates are both functional and aesthetically satisfying, complete with subtle branding. While a small part of the build, their quality ensures durability and protection for the upgraded braking system.
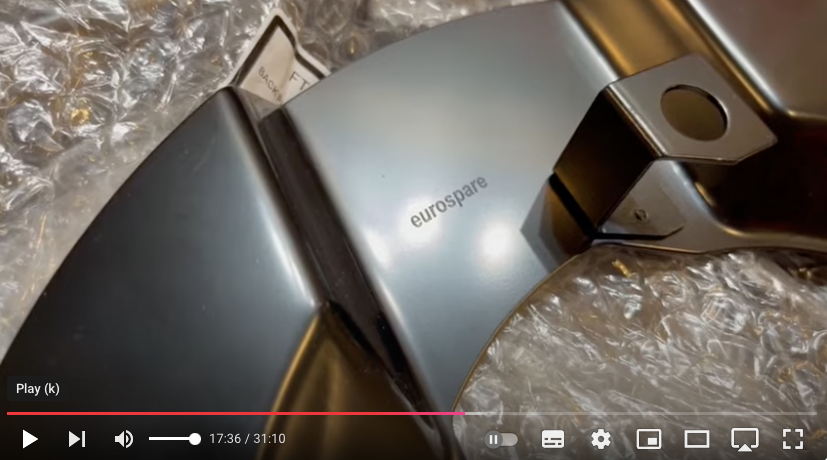
Finally, this week highlighted the importance of the right tools:
Thread Tap: Essential for cleaning out galvanization and powder coat from threaded holes. Without this step, bolt misalignment could jeopardize structural integrity.
Bodywork Hammers and Dollies: Used to clean and reshape the seat box for proper alignment with the bulkhead.
Pop Rivet Gun: Key for reattaching the battery box and reinforcing panels.
From precise differential sealing to thoughtful chassis modifications, every detail contributes to the larger vision of a high-performance, rally-ready vehicle.
Thank you for following along with Project Purdey! Stay tuned for more updates!
Watch the episode: